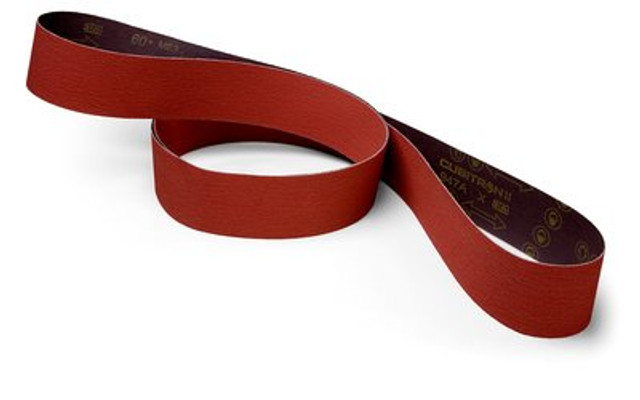
3M Products & Supplies
3M Cubitron ll Cloth Belt 947A, 40+ X-weight, 1 in x 12 in, Fabri-lok, Single-flex
Fast and Flexible
A closed coat and a grinding aid make our 3M Cubitron II Abrasive Belt 947A an outstanding option for low to medium pressure applications on heat sensitive metals. The nature of the abrasive structure diverts heat to the swarf, keeping both belt and workpiece cooler. It is now available in grades 40+ (make to order), 60+, 80+ and now 120+ adding an improved solution for finer finishing applications.
Cutting Edge Performance for Low and Medium Pressure Sanding
A semi flexible Cubitron II belt the 3M 947A sports an X-weight poly-cotton backing. Among backing weights, an X-weight cloth is flexible and provides tensile strength as well.
A great number of small belt sizes which are nimble and maneuverable so operators can get in, over and around intricate parts. These belts are good options for low-and-medium-pressure offhand operations for use on the following equipment:
How 3M Precision-Shaped Grain Works
3M Precision-Shaped Grain is designed to continuously fracture to form sharp points and edges that easily “slice” through metal. It cuts faster, lasts longer and stays cooler.
Conventional ceramic abrasive grain tends to “plow” through the metal, causing heat to build up in the workpiece and the abrasive – resulting in a slower cut, shorter belt life and undesirable effects, such as burnishing.
3M Science. The Beginning of Cubitron II.
In 2009, 3M scientists had long believed abrasives would work better if each grain of the ceramic abrasive material was exactly the same size and shape. It would act more like a knife shaving off material and less like a plow bouncing along the surface, creating heat damage. The breakthrough came when they realized they could use microreplication technology 3M was already using to create reflective material for signs, and other purposes.
Within a short time, they had created 3M's Precision Shaped Grain — identical triangular-shaped abrasive grains electrostatically oriented and distributed uniformly on an abrasive backing. The end result is faster, cooler cutting action, improved productivity, less operator fatigue and longer belt life.