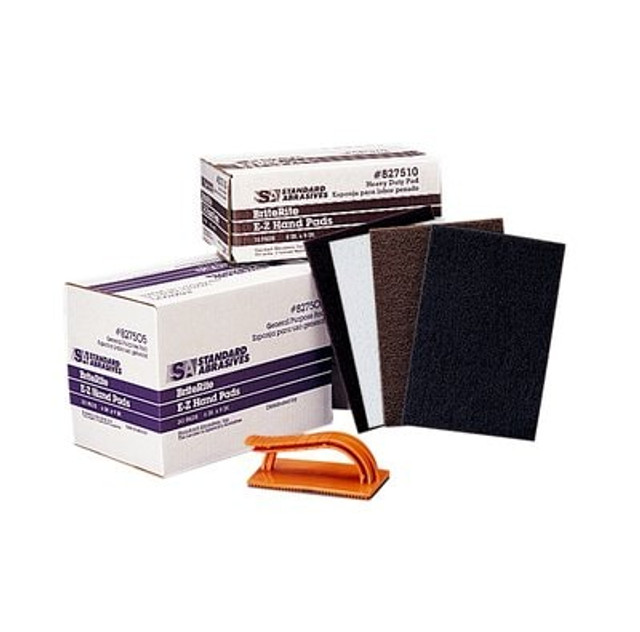
3M Products & Supplies
Standard Abrasives Buff and Blend GP Power Pad, 827600, 6 in x 9 in, A VFN, 50 ea/Case
Versatile Pad, Consistent Results
Our Standard Abrasives™ Buff and Blend Power Pad is designed to help you achieve consistent results on solid surfaces, painted panels, and other materials. Used by hand or on a power tool such as a jitterbug, these pre-cut pads are suitable for many applications, such as:
This versatile pad features a non-woven 3D web of fibers that conforms to irregular surfaces for a clean, consistent finish without cutting into the base material. For long-lasting utility, the open web is load and heat resistant, and the pad can be washed for re-use. An alternative to steel wool, it provides consistent results without rusting or leaving steel splinters behind.
Choosing the Right Buff & Blend Material
We make Power Pads with two mineral options to suit different application requirements: very fine grade aluminum oxide and very fine grade silicon carbide. Aluminum oxide offers a more aggressive cut and longer use, while silicon carbide typically provides a finer finish.
Each of the Standard Abrasives Buff & Blend materials offers unique benefits. Standard Abrasives™ Power Pads are offered with GP, HP and HS material.
GP is a general purpose material that delivers a high cut rate and consistent finish. It is the most middle-of-the-road, multi-purpose material among all the standard abrasives buff & blend materials. It's great for general-duty applications such as intermediate cleaning, blending, deburring and finishing - striking a balance between aggressive cutting action and fine finishing.
HP material is ideal for deburring and heavy edge work. Its durable construction gives it an aggressive cut and makes it suitable for edge deburring on aluminum extrusions, deburring aluminum die cast flashing, removing heavy surface oxidation, and the like.
HS is high strength material with increased tear-resistance, so it's a good match for light deburring and final finishing on irregularly-shaped parts, because it will not break down or fray when it comes in contact with contours and extrusions. It is an excellent choice for high luster and decorative finishes, and tasks such as final finishing on non-ferrous die cast molded parts, finishing on all metals and plated plastics, and polishing pipe threads and edges of molded glass containers.
Load-Resistant Material Boosts Life and Performance
Standard Abrasives™ Buff and Blend material is load-resistant to keep you cutting with fresh mineral. The gaps in the open web allow unwanted swarf to escape. Consequently, less debris clogs the abrasive, so the mineral can stay fresh, keep cutting sharp and deliver a consistent cut over the life of the product. As the fibers break down and fresh mineral is exposed, it reduces the likelihood of dull or blunt mineral smearing the surface, contributing to cleaner surfaces and less re-work. Furthermore, manual fatigue that may result from applying heavy pressure to a dull abrasive is reduced.
The Many Benefits of Standard Abrasives™ Buff and Blend Products
Standard Abrasives™ Buff and Blend products invigorate deburring, cleaning, blending and finishing applications by helping operators reduce finishing steps, minimize costs and achieve greater throughput. Each Buff and Blend product and grade offers unique benefits, so operators can choose from a versatile range of options to ensure optimal performance on specific applications.