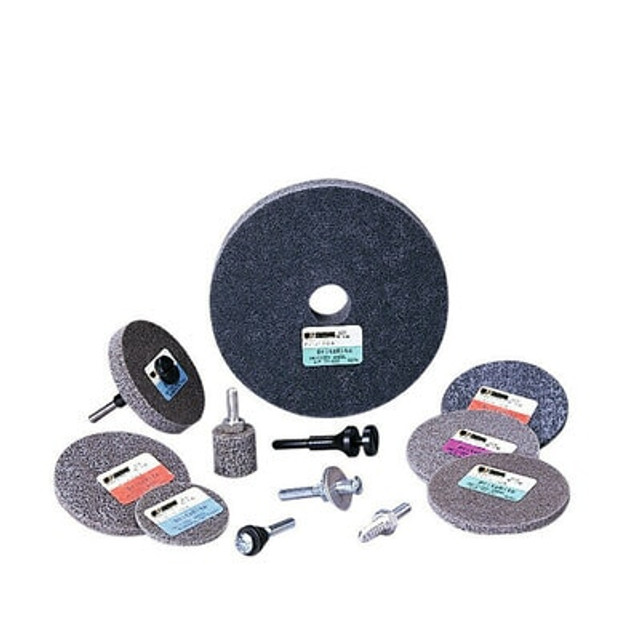
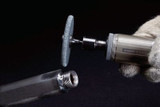
3M Products & Supplies
Standard Abrasives Quick Change TR A/O Unitized Wheel 852198, 521 3 in x 1/4 in, 10 ea/Case
Soft Density Wheel Offers Multi-Purpose Utility
Among Standard Abrasives Unitized Wheels, the 500 Series provides the softest density, and is available in medium (MED) and fine (FIN) grades suitable for light-weight cleaning, blending, and finishing. Use our Standard Abrasives Aluminum Oxide Unitized Wheel 500 Series wheels for general purpose cleaning or cleaning prior to painting. Trust them to effectively remove rust discoloration from welds, and remove minor pits and scratches, as well as lightweight resins or adhesives overspray and coating. They are a good match for polishing fillet areas on jet blades and soft metals prior to the coating process. Due to their conformability, these wheels are great for projects with strict tolerances, because they respond to surface irregularities.
Quick Change Wheels Increase Throughput
Standard Abrasives Quick Change Unitized Wheels are available in smaller sizes with a TS or TR attachment. Quick change wheels allow tool-free swap outs, maintain secure attachment at high speeds, and save operators time when switching discs between grades or applications. Easy fastening and swapping of wheels enhances tool efficiency and worker productivity.
Choose the wheel compatible with your TR or TS holder pad. TR wheels have a nylon threaded male hub that easily threads onto TR or 3M Roloc type holder pads with a turn of the wrist, and the TS system has a metal hub that fastens to its holder pad with a simple twist.
All Standard Abrasives TS and TR holder pads have a 1/4-20 female thread. A 1/4" TA4 mandrel attaches the holder pad to the tool (sold separately, part number 540013).
Non-Woven Unitized Construction Offers a Step Up in Density and Durability for Stubborn Surfaces
Standard Abrasives Unitized Wheels are a great match for tough deburring, cleaning, blending and finishing applications. They come in a broad range of densities and grades to suit different metals, the degree of aggressiveness required, shape of the part, and desired finish. Although used for some of the same tasks as Standard Abrasives Buff and Blend products, they are designed with a far stronger and denser construction to support more aggressive applications and accomplish material removal more rapidly. Even though unitized wheels are much stiffer products, the non-woven nylon fibers of the wheel maintain the advantage of responding to surface irregularities while preserving the geometry of the piece, and produce a consistent finish.
Unitized wheels are created by starting with layers of open web material that combines non-woven fiber strands and abrasive mineral with a tough resin bond. These layers of web are then cured and compressed together. By fusing layers of open web, the abrasive gains more toughness and durability, so it can withstand repeated wear.
Ultimately, the wheel's durability is what makes it such a good match for edges. Regardless of the diameter or thickness of the wheel, it maintains its structural integrity to remain a stiff and long-lasting abrasive. Additionally, as the layers wear, the wheel can be dressed to maintain its shape.
Load-Resistant Construction Boosts Life and Performance
Standard Abrasives Unitized Wheels are load-resistant to keep you cutting with fresh mineral. The gaps in the open web allow unwanted swarf to escape. Consequently, less debris clogs the abrasive, so the mineral can stay fresh, keep cutting sharp and deliver a consistent cut over the life of the product. As the fibers break down and fresh mineral is exposed, it reduces the likelihood of dull or blunt mineral smearing the surface, contributing to cleaner surfaces and less re-work. Furthermore, manual fatigue that may result from applying heavy pressure to a dull abrasive is reduced.
The Many Benefits of Standard Abrasives Non-Woven Products
Standard Abrasives Unitized Wheels offer many benefits for heavy-duty jobs. For all the aforementioned reasons, Standard Abrasives Unitized Wheels invigorate deburring, cleaning, blending and finishing applications by helping operators reduce finishing steps, minimize costs and achieve greater throughput.